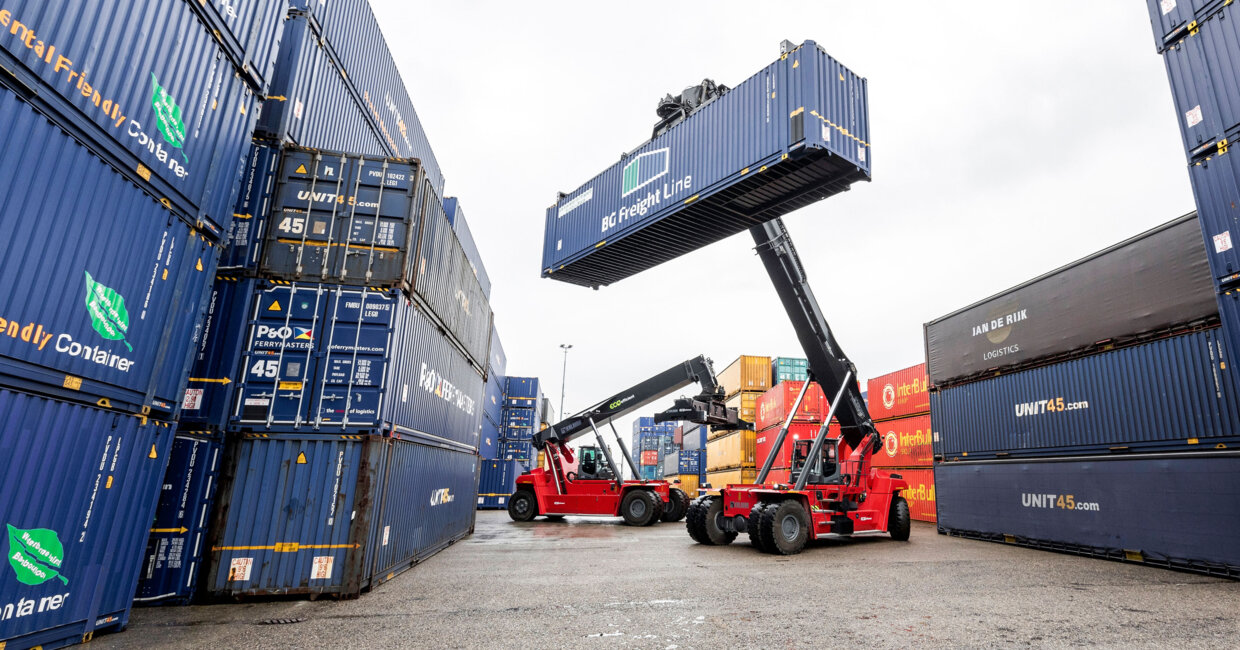
Towards eco-efficient cargo handling operations, part 2: Creating an infrastructure strategy
In this article series, we examine Kalmar's recommended step-by-step approach to eco-efficient cargo handling operations. In part 2, we discuss how to create a long-term strategy for the infrastructure and charging solutions required by electric-powered cargo handling equipment.
As terminals and logistic operators around the world turn to eco-efficient solutions in order to meet stakeholder requirements and internal emissions reduction targets, one of the biggest questions facing operators is how to design the infrastructure of their site. A key decision point is picking the best power options for future cargo handling equipment, while making use of renewable energy generation whenever possible.
“It all starts with understanding your way of working at the terminal, intermodal or logistics centers. Then you can align your operational, financial and eco-efficient targets with the solutions available in the market. In that way you can prepare your short, mid and long-term strategy,” says Christopher Saavedra, Terminal Design Services Manager at Kalmar.
Today, the potential power options for container and cargo handling equipment range from conventional diesel, biodiesel and compressed natural gas (CNG) to emerging fuels such as Hydrotreated Vegetable Oil (HV100) and hydrogen, all the way to fully-electric equipment. HV100 and hydrogen offer significantly lower emissions than diesel or CNG, but depend on new manufacturing and distribution infrastructures that are not yet in place worldwide. On the other hand, fully-electric solutions powered by renewable energy enable close to zero on-site emissions, but demand a robust and well-planned charging system.
Electric solutions gain ground
The demand for electrically powered cargo handling equipment has grown rapidly over the last few years. "We have had electric forklifts since the 1980s, but the real boom started in 2019 when we launched our first medium-sized electric forklift truck," says David Piltén, Business Development Manager, Kalmar Forklift Trucks. "Eco-efficiency is very high on companies' agenda these days, and electric forklift trucks are on the way to becoming the most popular option with our customers."
"Eco-efficiency is very high on companies' agenda these days, and electric forklift trucks are on the way to becoming the most popular option with our customers."
Arguably, the most crucial question for designing the infrastructure for electrically powered machines is ensuring adequate charging capacity for not only the current fleet, but also projected future operations. "At the moment, equipment charging is still contact-based, though we are looking into various wireless or inductive charging solutions," says Piltén. "In the nearer term, we are also exploring options for autonomous or automatic charging that does not require the operator to exit the machine to connect the charging cable. These are developments that we expect to see deployed over the next few years."
Alongside charging solutions, battery technology is advancing with great strides, driven by the mass-market electric car industry. "The last two to three years have seen the introduction of several new battery chemistries that will become increasingly economical as manufacturing volumes ramp up," notes Piltén.
“To answer those main questions – the number of charging stations needed for your fleet and the best location for them – Kalmar has developed simulation and emulation capabilities to verify the operational handling concepts and evaluate the different alternatives based on the customer layout,” says Christopher Saavedra.
Taking charge of charging
Whatever the charging or battery solution, all-electric operations require a markedly different approach to infrastructure planning from traditional solutions. "You need to be aware of your fleet and its requirements in much more detail," says David Piltén. "If you add some machines to a diesel-powered fleet, you can just install an extra tank of diesel. With electric machines, you have to ensure that the entire power grid can keep up with your requirements. How many electric machines will you be running, and how many of them will be charging at the same time? All this needs an in-depth analysis."
Typically, to even the load on the power grid, all-electric cargo handling infrastructures will use some type of on-site electricity storage. The Kalmar ChargePod is a container-based mobile equipment charging solution that is easy to install, requires minimal space and can be positioned wherever it is needed. "The ChargePod is perfect for customers that have limited space indoors, and it can greatly simplify the transition to electrification," Piltén notes.
Seeing the big picture
Whether the infrastructure is built around all-electric equipment or a future fuel source such as hydrogen, the four key factors when designing an eco-efficient infrastructure can be summarized as availability, manageability, cost and sustainability. Are the required energy sources available, and what are the short and long-term plans for electricity generation and grid capacity? Are there restrictions governing the handling of alternative energy sources or high-voltage electrical equipment? What are the installation and lifecycle costs and savings of the solution? And, finally, what is the overall sustainability impact of the chosen approach?
"The path that operators need to take in order to reach their eco-efficiency targets varies greatly between regions and individual terminals," says Marcelo Goncalves, Director, Kalmar Latin America. "For example, in Latin America, we have 33 countries with very different economies and levels of infrastructure. Some countries such as Brazil are already quite far in the demand for electric equipment and the use of renewable energy, while others still have a longer way to go. However, typically in this region it's not legislation that drives companies towards eco-efficiency, but the desire to proactively take the first steps in the market and be ready for a greener future."
"We need to understand that there is no one size fits all solution when it comes to eco-efficient solutions. There are different challenges and local legislations for every region and customer,” adds Christopher Saavedra.
"Terminals face widely differing government policies and eco-efficiency drivers in their respective countries, so every situation is unique, but we are there to help our customers in these discussions right from the beginning."
Links in the chain
To realize the full potential of eco-efficient solutions and to gain the maximum potential for reducing emissions, it's essential to consider how the energy that powers operations is generated. Ideally, electricity would be generated sustainably from solar, wind or other renewable power sources that feed into the grid.
At the port or terminal power station, additional renewable energy can be produced using solar panels. If production exceeds consumption during sunlight hours, energy can be stored in battery packs, from which it can be drawn at times when green electricity is not available from the grid. Additionally, the battery storage can also help in reducing peak usage and costs from the local grid during the day.
At the site, the sustainable energy is transferred to the local on-site power grid from which the operational cargo handling equipment is then charged. When the system is designed as a complete infrastructure, the result is a sustainable electric energy value chain that encompasses everything from renewable power sources to on-site charging management and even Li-ion battery recycling.
"Electrification is definitely the future, and the market has already understood that this is the path we need to follow," says Marcelo Goncalves. "Especially at ports with a lot of activity, the charging strategy and infrastructure needs to be thought out very carefully. Terminals face widely differing government policies and eco-efficiency drivers in their respective countries, so every situation is unique, but we are there to help our customers in these discussions right from the beginning."
Related articles
Further reading
Subscribe and receive updates in your email
Meld je aan voor onze publicaties